What Is Lean?
March 4, 2025
Unlock the power of Lean! Discover what is Lean, its principles, and its transformative impact on businesses.
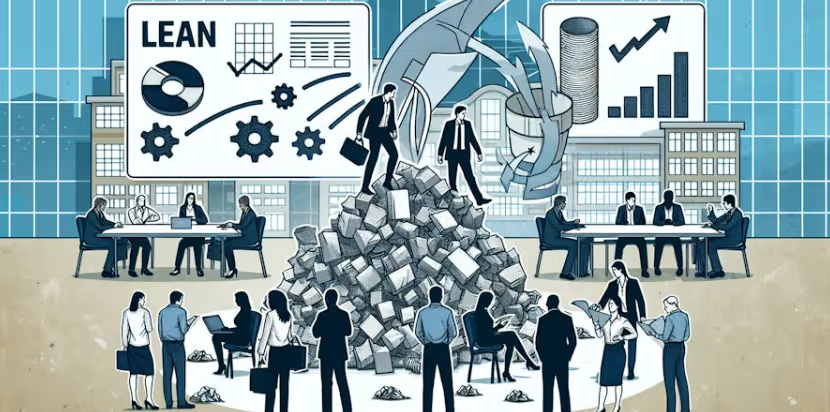
Understanding Lean Principles
Unveiling the answer to 'what is lean?' requires diving into its foundational principles. This approach is applied in various business contexts to enhance productivity, reduce waste, and optimize resources.
Lean Management Overview
Lean management is a strategic approach that focuses on delivering value to customers by improving business processes and fostering a culture of continuous improvement. It aims to eliminate waste and streamline operations for efficiency, productivity, and sustainable competitive advantage. It also emphasizes the importance of employee engagement and empowerment iObeya.
At its core, lean management is about creating more value with fewer resources. It pushes organizations to question traditional business practices and find innovative ways to meet customer needs. This approach can be applied to operational improvement in any industry, including transportation, professional services, retail, healthcare, construction, maintenance, and software development KaiNexus Blog.
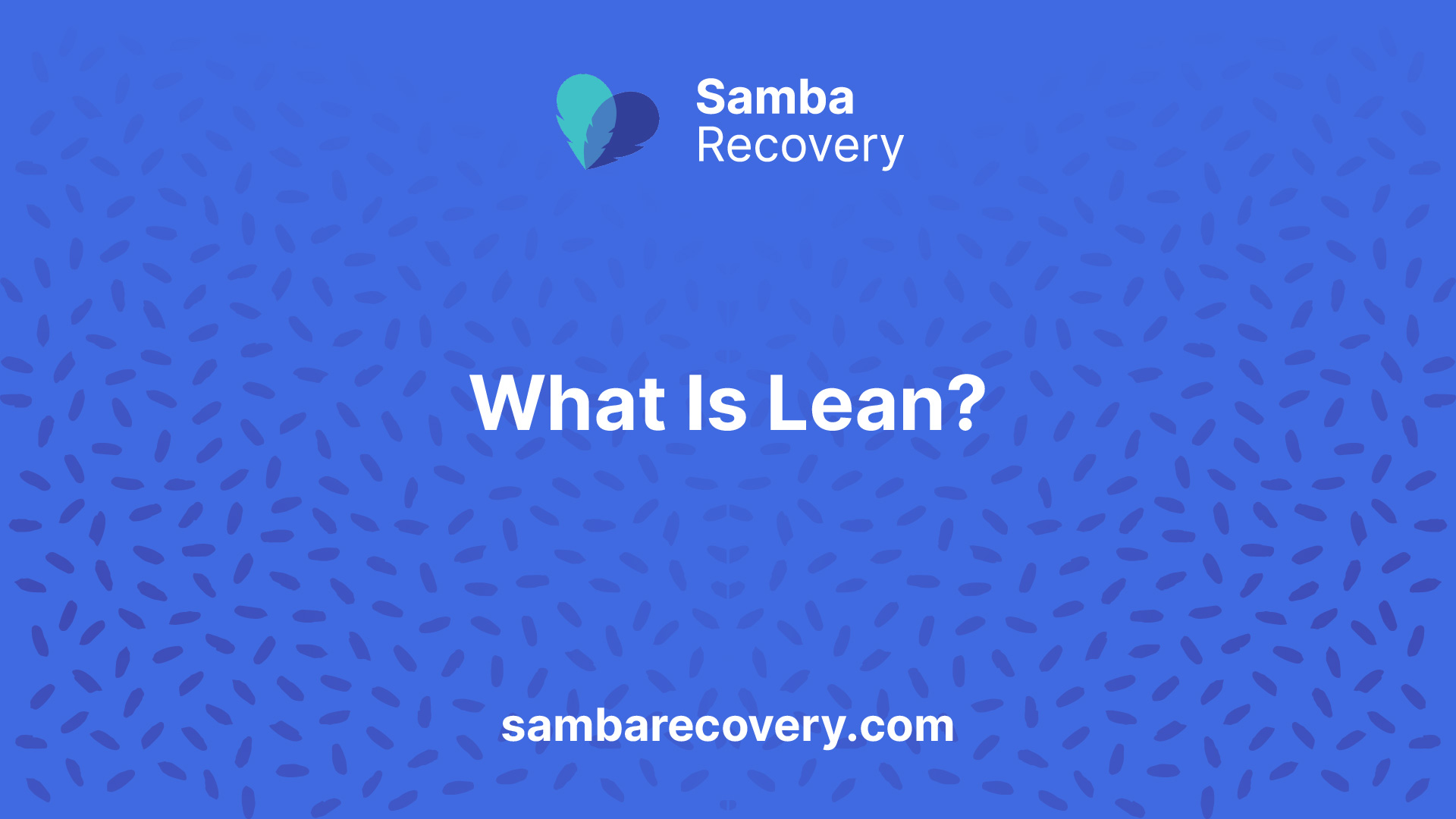
Lean Methodology in Project Management
In the realm of project management, lean takes on a specific form. Known as Lean Scrum, this methodology aims to eliminate waste and increase productivity through multiple waste elimination cycles. It helps organizations reduce product development cycles and enhance efficiency Simplilearn.
Lean encourages the establishment of a smooth flow, avoidance of bottlenecks, and strategies such as cross-functional collaboration and multi-skilled employees to ensure efficient operations. It is a customer-focused methodology that strives to deliver optimal products or services in the most efficient manner possible Simplilearn.
Moreover, lean thinking and practice can significantly enhance various aspects of an organization. It can aid executive coaching in strategy development, engage employees to create a problem-solving culture, and improve organizational performance through different areas such as operations, product & process development, and administration & support Lean Enterprise Institute.
In summary, lean principles provide a robust framework for organizations seeking to enhance efficiency, productivity, and customer satisfaction. It is a versatile approach that can be tailored to meet the unique needs and goals of any business.
Core Principles of Lean
The principles of Lean form the foundation of the Lean methodology, guiding its processes and strategies. They are the pillars that answer the question of "what is Lean?" and provide insight into how organizations can streamline their operations for maximum efficiency.
Defining Value in Lean
The first principle of Lean revolves around defining value. This is not a value as dictated by the organization but by the customer. According to Lean, the value of a product or service is determined by what the customer is willing to pay for it. Understanding this value is critical as it informs the entire production process, ensuring operations are aligned with customer demands and expectations.
Mapping the Value Stream
Once value has been defined, the next step is to map the value stream. This involves identifying all the steps involved in the production process, from raw materials to the finished product. The goal is to eliminate all activities that do not add value to the customer, thereby reducing waste and improving efficiency. Lean companies are typically organized by value stream, which allows value to flow quickly to the customer at low cost and with excellent quality.
Creating Flow in Lean
Creating flow is another integral principle of Lean. This involves ensuring that value-adding activities flow smoothly without interruptions or delays. Strategies for creating flow include breaking down steps, reconfiguring production steps, leveling out workloads, creating cross-functional departments, and training employees to be multi-skilled and adaptive [3].
Establishing Pull System
Another fundamental principle of Lean is the establishment of a pull system. Unlike traditional manufacturing, which often relies on anticipated demand, Lean manufacturing focuses on real customer demand. Production is driven by what customers want, and organizations respond quickly to these demands. This pull system allows the Lean company to calibrate production to customer demand, pulling the right amount of materials and products through the various processes [2].
Pursuing Perfection in Lean
The final principle of Lean is the pursuit of perfection. This involves continuously improving processes, eliminating waste, and striving for excellence. The goal is not just to meet customer expectations, but to exceed them, delivering superior quality and value at every touchpoint.
These core principles of Lean provide a framework for organizations looking to enhance their operational efficiency and customer value. They underscore the central tenet of Lean: the relentless pursuit of efficiency and value, achieved through a customer-centric approach and continuous improvement.
Lean Implementation Strategies
Implementing Lean principles in an organization requires specific strategies that aim to improve efficiency and eliminate waste. These strategies are designed to establish a smooth flow, avoid bottlenecks, create cross-functional departments, train multi-skilled employees, and integrate a pull-based system.
Smooth Flow Establishment
A fundamental aspect of Lean is creating a flow that ensures value-adding activities operate smoothly without interruptions or delays. This establishment of a smooth flow is achieved by breaking down steps, reconfiguring production steps, and leveling out workloads. By doing so, organizations can achieve a seamless flow of operations, which significantly enhances productivity.
Avoiding Bottlenecks
Bottlenecks are obstructions in the workflow that cause delays and inefficiencies. Lean implementation strategies focus on identifying and eliminating these bottlenecks. By doing so, organizations can ensure a smooth and uninterrupted flow of operations, leading to improved efficiency and productivity.
Cross-Functional Departments
In a Lean company, teams are organized by value stream, which allows value to flow quickly to the customer at low cost and with excellent quality. This contrasts with traditional companies, which are organized in functional departments that often result in long lead times and poor quality [2]. Cross-functional departments enable better communication, collaboration, and problem-solving, contributing to the overall efficiency of the organization.
Multi-Skilled Employees
Another significant strategy in Lean implementation is the development of multi-skilled employees. Lean encourages training employees to be adaptive and acquire multiple skills, which increases their versatility and ability to handle different tasks. This not only improves the flow of operations but also fosters a culture of continuous learning and development.
Pull-Based System Integration
Lean manufacturing is based on the concept that production should be driven by real customer demand, not by anticipated demand. It focuses on creating what customers want and responding quickly to their demands. In contrast to traditional companies that produce things in batches controlled by Material Requirements Planning (MRP) systems, Lean organizations implement a pull-based system. This system allows the Lean company to calibrate production to the demand of the customer and pull the right amount of materials and products through the various processes [2].
These strategies play a vital role in the successful implementation of Lean principles. By embracing these strategies, organizations can significantly improve their operations, enhance customer satisfaction, and gain a competitive edge.
Benefits of Lean Practices
Understanding the benefits of lean practices can help businesses see the value in adopting this methodology. These benefits extend to customer satisfaction, efficiency and productivity, employee engagement, and competitive advantage.
Customer Focus and Satisfaction
At the heart of lean management is a focus on customer satisfaction. By identifying what creates value for customers, businesses can streamline their operations to deliver that value more efficiently and reliably. This customer-centric approach can lead to higher levels of customer satisfaction, fostering loyalty and promoting repeat business.
Increased Efficiency and Productivity
Lean practices also contribute to increased efficiency and productivity within organizations. By establishing smooth operational flows and avoiding bottlenecks, businesses can ensure their processes are as efficient as possible. Moreover, strategies such as deploying cross-functional departments and multi-skilled employees can further enhance operational efficiency [5].
Employee Engagement and Empowerment
Lean practice begins with the work and the people doing that work. By fostering a culture of ongoing experimentation and innovation, businesses can engage their employees and empower them to contribute to improvements in quality, flow, time, effort, and cost. This can lead to a highly adaptive organization characterized by systematic and continuous learning.
Sustainable Competitive Advantage
Adopting lean practices can also help businesses gain a sustainable competitive advantage. By improving efficiency and reducing waste, companies can offer better products and services at lower costs, thereby attracting and retaining customers. In addition, lean practices can help companies reduce their environmental impact, improve employee morale and engagement, and create value for customers, employees, and stakeholders [7].
In conclusion, the benefits of lean practices can be significant, spanning various aspects of a business from customer satisfaction to operational efficiency, employee engagement, and competitive advantage. By understanding these benefits, businesses can make informed decisions about whether and how to implement lean practices in their operations.
Evolution of Lean Thinking
Understanding the evolution of lean thinking is crucial in grasping what is lean? The approach has evolved considerably since its inception and is now a widely accepted methodology across various industries.
Lean Beyond Manufacturing
Although Lean management is an adaptation of the Toyota Production System, which was implemented to improve the efficiency and flexibility of manufacturing operations post-World War II (KaiNexus Blog), it has now transcended beyond the confines of manufacturing.
The principles and practices of lean have been adapted and applied to various aspects including executive coaching in strategy development, engaging employees to create a problem-solving culture, and enhancing organizational performance through different areas such as operations, product & process development, administration & support, problem-solving, coaching, executive leadership, and line management.
Lean in Various Industries
Lean thinking has been adapted to various industries such as healthcare, construction, logistics, distribution, government, and software development. Operational improvement in any industry, including transportation, professional services, retail, healthcare, construction, maintenance, and software development can be achieved by applying lean management.
This wide application testifies to the universal relevance of lean principles. Whether it's reducing waste in a manufacturing process, improving patient care in a hospital, or streamlining software development, lean thinking offers a structured approach to enhance efficiency and productivity.
Continuous Improvement Mindset
Central to the evolution of lean is the promotion of a continuous improvement mindset. Lean methodology demands constant fine-tuning and refinement of processes to bring value to the customer.
This continuous improvement mindset allows organizations to adapt and evolve in response to changing market demands. It encourages constant learning and growth, fostering a culture where employees are not only reactive to problems but proactive in identifying and addressing potential issues before they arise.
In essence, the evolution of lean thinking is a testament to its effectiveness and adaptability. From its roots in manufacturing to its application in various industries and its promotion of a continuous improvement mindset, lean has proven to be a powerful tool for enhancing value and efficiency in any organization.
Real-Life Examples of Lean Success
Understanding 'what is lean?' in theory is essential, but seeing this methodology at work in real life provides a more tangible perspective. Let's look at how lean principles have impacted major companies and different sectors and explore the benefits realized from lean implementation.
Lean Impact on Major Companies
Several well-known companies have embraced the lean philosophy, resulting in significant improvements in their production processes, quality control mechanisms, and overall business operations.
- Toyota: One of the pioneers in adopting lean ideology, Toyota's focus on eliminating waste and minimizing faulty products through processes like Jidoka (automation with human assistance) and the Just In Time (JIT) model has been instrumental in shaping their successful manufacturing processes.
- Intel: By implementing lean manufacturing techniques, Intel managed to reduce the time to bring a microchip to the factory from over three months to less than ten days. This focus on quality control and waste reduction has enhanced profits and customer satisfaction.
- John Deere: The adoption of lean manufacturing led to fully automated quality control mechanisms at John Deere, enabling more efficient defect checks, increased daily supply output, lower consumer prices, and avoiding unnecessary material wastage [10].
- Nike: Implementing lean manufacturing resulted in reduced waste and improved customer value at Nike. It also led to a significant decrease of up to fifteen percent in poor labor practices at their overseas manufacturing plants, by valuing workers more in the production process.
Lean Practices in Different Sectors
Lean principles aren't exclusive to manufacturing; they're applicable to any sector that can benefit from streamlined processes, waste reduction, and value maximization. Industries ranging from healthcare to information technology to logistics are increasingly adopting lean methodologies, aiming to reduce waste and maximize customer value. This has led to beneficial effects on both consumers and businesses, enhancing efficiency and productivity.
Lean Implementation Benefits
The benefits of lean implementation are both tangible and intangible. On one hand, tangible benefits include cost reduction, increased efficiency, improved product quality, and enhanced customer satisfaction. On the other hand, lean implementation brings about intangible benefits like a culture of continuous improvement, employee engagement and empowerment, and a sustainable competitive advantage. By aligning the organization's processes, people, and purpose towards value creation, lean implementation fosters a conducive environment for business excellence.
References
[2]: https://www.lean.org/the-lean-post/articles/ask-art-how-is-traditional-management-different-from-lean-management/
[3]: https://theleanway.net/The-Five-Principles-of-Lean/
[4]: https://www.iobeya.com/blog/5-key-benefits-lean-management/
[5]: https://www.simplilearn.com/5-lean-principles-article
[6]: https://www.lean.org/explore-lean/what-is-lean/
[7]: https://www.amper.xyz/post/lean-manufacturing-examples
[8]: https://www.easyagile.com/blog/lean-methodology/
[9]: https://blog.kainexus.com/improvement-disciplines/lean/what-does-the-concept-of-lean-mean-in-business/
[10]: https://refinedimpact.com/4-good-examples-of-companies-that-use-lean-manufacturing/
About Samba Recovery
Start your treatment today!
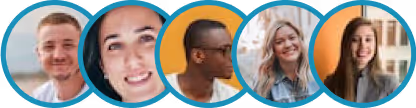
Featured Articles
Read the latest addiction news and recovery tips from our blog.
Samba Recovery never miss an opportunity
Substance abuse doesn’t have to be a life sentence! Sustainable recovery is possible and the best version of youself awaits at our Atlanta and Savannah, Georgia addiction recovery center.
We’ll help you learn that the opposite of addiction is connection. We’ll give you skills to discover your self-worth and show you the tools for a life of hope and promise.
Contact us today!
We accept most major insurances
We partner with most major insurances, enabling you to access premier therapy services.
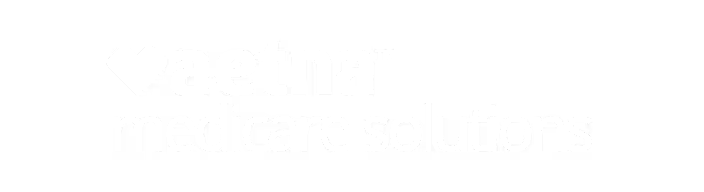
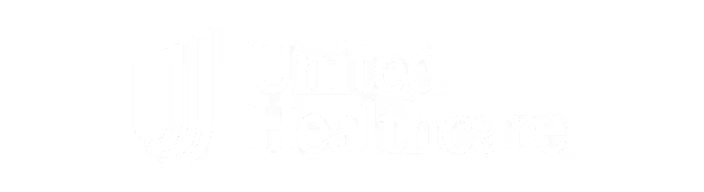
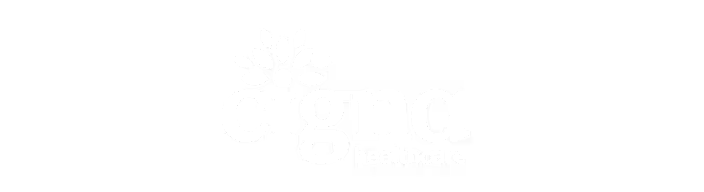
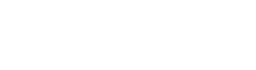
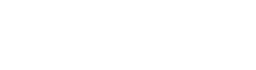
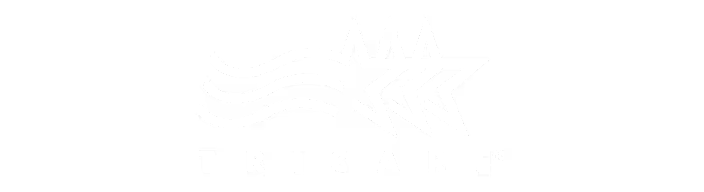